Trong quá trình Khoan, có lẽ không có yếu tố nào quan trọng hơn Vật liệu Gia công (Workpiece materials). Nó là yếu tố quyết định Hình dạng và chất liệu mũi khoan (Drill Geometry and Substrate), lớp phủ cần thiết (Coating), chất làm nguội (Coolant), tốc độ và bước tiến (Speeds and Feeds).
Nhôm được biết đến là một Kim loại mềm và dẻo, tuy nhiên, sự ngộ nhận về cách xử lý Nhôm đang hiện hữu khá nhiều trong những ai chưa thực sự tìm hiểu kỹ về nó.
Theo ông Elliott Frazier (Product Manager của Tungaloy America Inc.), “Nhôm được biết đến là một trong những vật liệu dễ gia công nhất, nhưng ngược lại, nó có những đặc điểm rất riêng biệt”. “Thông thường, Nhôm có đặc tính khá mềm và dẻo, là vật liệu không màu (Non Ferrous) với tỷ trọng thấp (Low density) và khả năng chống mài mòn cao. Cái khó của quá trình khoan Nhôm chính là do độ dẻo và mềm của nó, khiến vật liệu phải tiếp xúc liên tục và kéo dài với mặt thoát phôi (Rake face) và các góc cắt (Cutting Edges) của mũi khoan”.
Cạnh, Lưỡi cắt, và Lớp phủ
“Có 2 yếu tố quan trọng khi khoan Nhôm, chính là Sự tạo phôi và Sự thoát phôi", ông Chad Lynch (Sales Engineer của AMEC) giải thích, “Nếu chúng ta khoan Nhôm sử dụng Mũi khoan có hình dạng, lớp phủ không phù hợp cùng với quá trình làm nguội không đúng cách, khả năng cao sẽ tạo ra những phôi sợi dài ngoằn ngoèo quấn quanh Mũi khoan và làm tắc nghẽn quá trình khoan”.
Ông Frazier giải thích thêm, “Khi tình huống đó xảy ra, phôi Nhôm tạo ra sẽ dồn lên và với nhiệt độ cao, khiến chúng dính chặt vào các cạnh cắt và ngăn cản quá trình tạo phôi mới, lúc đó, phôi sẽ bị đầy và gây nghẽn lưỡi cắt”.
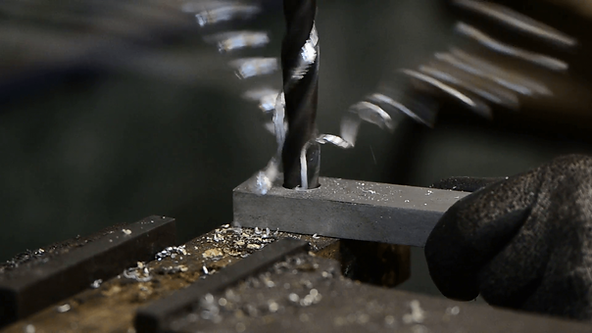
Hình 1: Phôi thoát dạng sợi (String out)
“Phôi Nhôm thường có xu hướng “thoát dạng sợi (string out)” bởi đặc tính mềm của nó", ông Lynch chú thích, “Và cách để xử lý nó là nhờ vào Hình dạng của Mũi khoan (Drill Geometry), mũi khoan với độ xoắn cao hơn (higher rake) sẽ tạo nhiều đường cắt hơn và ép phôi vào những vị trí có tác động mạnh (lực cắt mạnh) của Mũi khoan”.
“Sự khác nhau lớn nhất giữa khoan Nhôm và những vật liệu cứng hơn, chính là điểm cắt (Shear point) của Nhôm thấp vừa đủ để các góc cắt của Mũi khoan có thể cắt/thái lát chúng ra, và điều đó ngược lại với vật liệu cứng, khi mà phôi cần phải được đẩy ra ngoài hoàn toàn nguyên mảnh. Do đó, Mũi khoan với hình dạng Góc trượt (Shear angle) lớn và thẳng đứng với độ mài cạnh nhỏ nhất sẽ tối ưu cho quá trình khoan Nhôm”, theo ông Jason Hout (Sandvik Coromant Co.).
“Thông thường, mũi khoan với độ xoắn cao (high Helix angle), mặt lưỡi trơn bóng (polished Flutes), góc cắt (Point angle) 130 ~ 140 độ sẽ tối ưu hoá khả năng thoát phôi và hiệu suất gia công. Tuy nhiên, do Nhôm có đặc tính khá mềm, khoan Nhôm với mũi khoan thông số trên có khả năng sẽ gây khó khăn cho việc giữ ổn định đường kính lỗ khoan (dung sai tăng) và bề mặt thành lỗ. Trong trường hợp độ chính xác của đường kính lỗ khoan và bề mặt thành lỗ là yếu tố cần thiết, lựa chọn mũi khoan với lưỡi cắt thẳng và lỗ tưới nguội xuyên (Through-coolant Drill) sẽ phù hợp”.
Thêm một yếu tố cần lưu ý khác, góc cắt nhọn sẽ có đặc tính yếu hơn các góc chuẩn, và có khá nhiều loại Nhôm trên thị trường có thành phần Silica cao (các hạt cứng-như thuỷ tinh trong hỗn hợp của Nhôm có thể phá vỡ góc cắt của dụng cụ gia công). Do đó, đối với những loại Nhôm có đặc tính chống mài mòn cao (Silica) này, cách xử lý là tráng phủ (coating) thêm lên Mũi khoan, hoặc bằng cách khác, chuyển sang dòng Hợp kim (Carbide) hoặc PCD.
Khi chuyển đổi sang các dòng Hợp kim, hãy lưu ý tránh việc lựa chọn các mũi có lớp phủ có thành phần Nhôm (Aluminum-based coating), bởi vì thành phần Aluminum sẽ có xu hướng dính vào bề mặt của vật liệu gia công. Các lớp phủ phổ biến như Al203 hoặc AlTiN, khi đưa vào gia công dưới nhiệt độ cao và áp lực của quá trình gia công, lớp phủ (bao gồm Al) ấy không những phản ứng với vật liệu gia công (Nhôm), mà còn tạo phản ứng hình thành hiện tượng lẹo dao (Build-up Edge BUE). Thay vào đó, hãy sử dụng lớp phủ có thành phần TiB2 (Titanium Diboride) hoặc Amorphous Diamond Film (ví dụ như DLC hoặc PCD), khuyến khích bởi ông Hout.
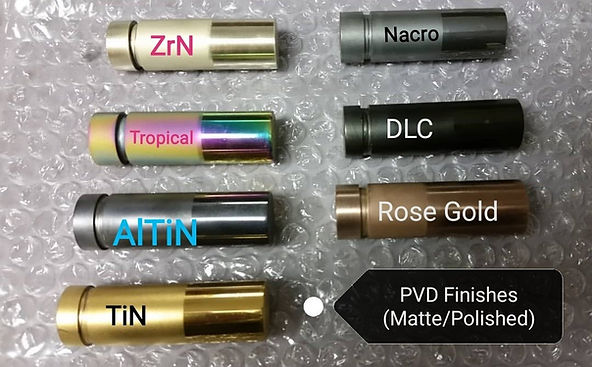
Nếu các lớp phủ này không phù hợp với một số điều kiện của Người sử dụng, Hợp kim không phủ với bề mặt trơn bóng đã có thể đáp ứng hầu hết các ứng dụng trên Nhôm. Ngoài ra, ông Frazier lưu ý thêm, chúng ta có thể lựa chọn Mũi khoan Hợp kim Micrograin (hạt siêu vi) có độ cứng tầm 92~93 HRA cho các loại Nhôm có thành phần Silica thấp. Tuy nhiên, những loại Nhôm sử dụng trong Rèn hoặc Đúc thường có Silica trên 11%, vì vậy lựa chọn mũi hợp kim có lớp phủ PCD hoặc DLC sẽ tối ưu nhất.
Do các lớp phủ thông dụng trên thị trường hiện nay đều có thành phần Aluminum (Al) làm nền, nên các Dụng cụ cắt gọt (mũi khoan, taro, phay,...) ứng dụng cho Nhôm thường được khuyến khích sử dụng loại không phủ. Nhưng hiện nay các Nhà sản xuất đang phát triển lớp phủ Titanium-Zirconium-Nitride (TiZrN) nhằm tối ưu hoá hiệu suất khi gia công Nhôm. Một ví dụ từ ông John Lombardi (President của R.I. Carbide Tool Co.), “Chúng tôi có một Khách hàng cần khoan một lượt 3,000 lỗ trên một tấm Nhôm, nhưng chỉ cần 1 lỗ bị hỏng, nguyên tấm Nhôm sẽ buộc phải bỏ. Chúng tôi đã thử nghiệm nhiều lần và đưa ra được giải pháp tối ưu nhất bằng cách, lựa chọn loại mũi khoan có bề mặt siêu trơn (highly lubricious) với lớp phủ ZrN, và có lỗ tưới nguội xuyên (through-coolant drill), sau đó áp dụng chạy với tốc độ cao, chúng tôi đã đáp ứng được yêu cầu khắt khe đó của họ”.
Làm nguội (Cool down)
Khả năng đẩy phôi đi đôi với việc áp dụng tưới nguội phù hợp. Khoan Pecking luôn là kỹ thuật phổ biến, nhưng cũng có nhiều Người sử dụng muốn tránh việc rút mũi khoan khi có thể, do đó, lưỡi cắt trơn bóng (polished flutes) và lỗ tưới nguội xuyên (through-coolant) là yếu tố quyết định.
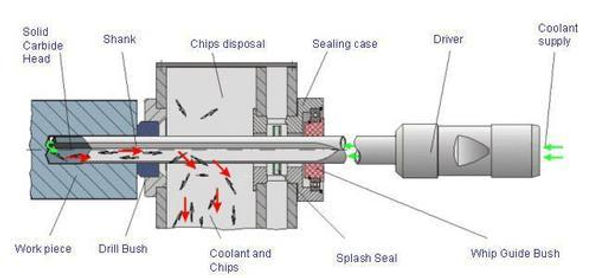
“Đặc biệt khi bạn cần khoan một lỗ sâu, yếu tố chính luôn là khả năng tưới nguội (coolant flow) nhằm đẩy phôi ra khỏi lưỡi cắt”. Khi gia công lỗ sâu, ông Frazier luôn khuyến khích sử dụng mũi khoan có lỗ tưới nguội xuyên, và ông giải thích rằng: “Để gia tăng Tốc độ cắt (Metal Remover Rates - MRR), quá trình tưới nguội liên tục là điều cần thiết nhằm đẩy phôi nhanh nhất có thể ra khỏi lưỡi cắt, và đặc biệt là MRR ở gia công Nhôm thường rất cao". Vì vậy, trong tình huống này, việc lựa chọn đặc tính mũi khoan và loại tưới nguội phù hợp là rất quan trọng. “Dòng tưới nguội càng cao, lực đẩy càng tăng và từ đó gia tăng năng suất".
Ông Frazier lưu ý thêm, “2 loại tưới nguội phổ biến trong gia công kim loại là Cutting Fluid (dầu cắt gọt pha nước) và Neat Cutting Oil (dầu cắt gọt không pha nước). Neat Cutting Oil thường tạo ra bề mặt gia công mịn, trong khi đó, Cutting Fluid có thể gây ra hiện tượng kết dính Nhôm trên thành lỗ khoan, tạo ra bề mặt ráp”.
Vì vậy, để tổng kết lại bài chia sẻ, với những Nhà sản xuất muốn tối ưu hoá tốc độ và hiệu quả gia công Nhôm, việc lựa chọn Mũi khoan và Chất tưới nguội phù hợp rất quan trọng (như đã giải thích ở trên). Vì Nhôm được cho là một trong những vật liệu rẻ và “dễ" gia công nhất, nhưng việc ngộ nhận đặc tính của nó sẽ khiến quá trình gia công trở nên khó khăn và kém hiệu quả. Như ông Frazier (Tungaloy America Inc.) chia sẻ, “nếu ngày càng nhiều Nhà sản xuất đổ bộ gia công những vật liệu thông dụng như Nhôm này, sự gia tăng cạnh tranh và biên lợi nhuận giảm chắc chắn sẽ không thể tránh khỏi. Do đó, điều quan trọng cần thiết cho các Nhà sản xuất tương lai chính là tối đa hoá tốc độ và hiệu quả khi gia công các loại vật liệu mang tính “cạnh tranh cao" này”.
Nguồn tham khảo:
Allied Machine & Engineering Corp.
Nachi America Inc.
Flowdrill Inc.
R.I. Carbide
Sandvik Coromant Co.
Tungaloy America Inc.